
Ureteroscope Driver
Subsystem device of Monarch Platform, Ureteroscopy FDA 510(k) April 2022
US Patent 11,246,672, WO Patent 2022175850
All information shared here is publicly available content

This single-use device drives a Ureteroscope shaft during minimally invasive robotic ureteroscopies.
I spent 4 years turning “we need to safely insert/retract a ureteroscope shaft at rapid speeds” into a product that enables that and more:
Ureteroscope alignment with an off-the-shelf ureteral access sheath
Adjustable “virtual” spring to increase or reduce wheel pinch force on the flexible shaft
Detection features to prevent the shaft from imparting too much force on the patient's anatomy
Space for a basketed kidney stone to be robotically ejected
Minimal backlash to enable easy maneuvering inside the patient
Auto-sensing of the flexible shaft presence
Top-loading capability
Speed-adjustable insertion
Unrestricted shaft roll
Automatic system detection of device installation
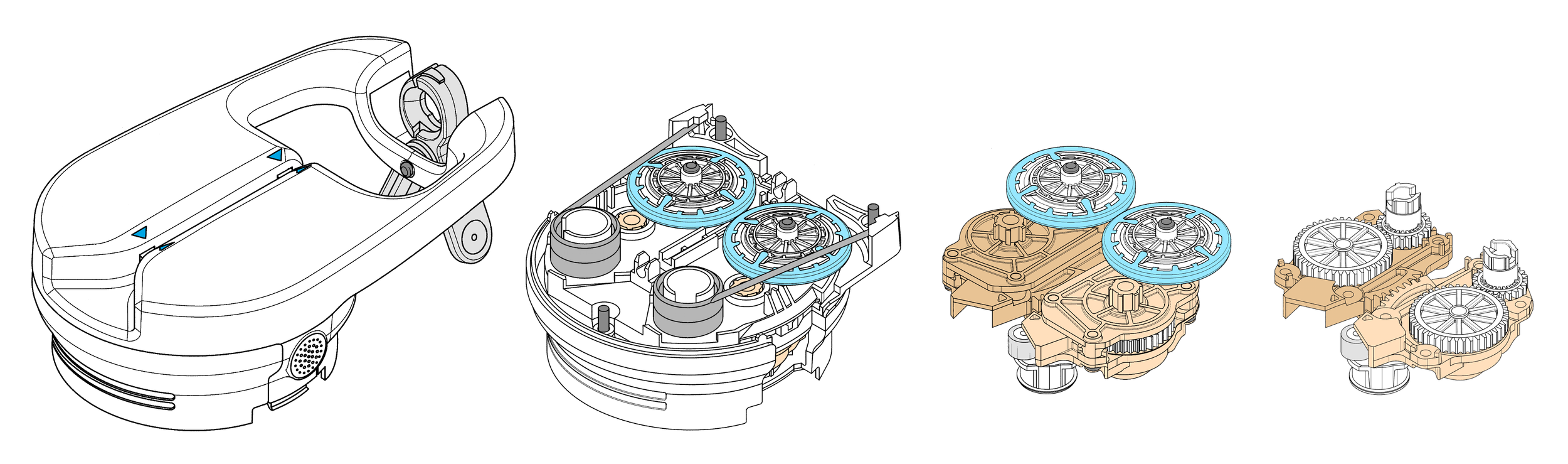
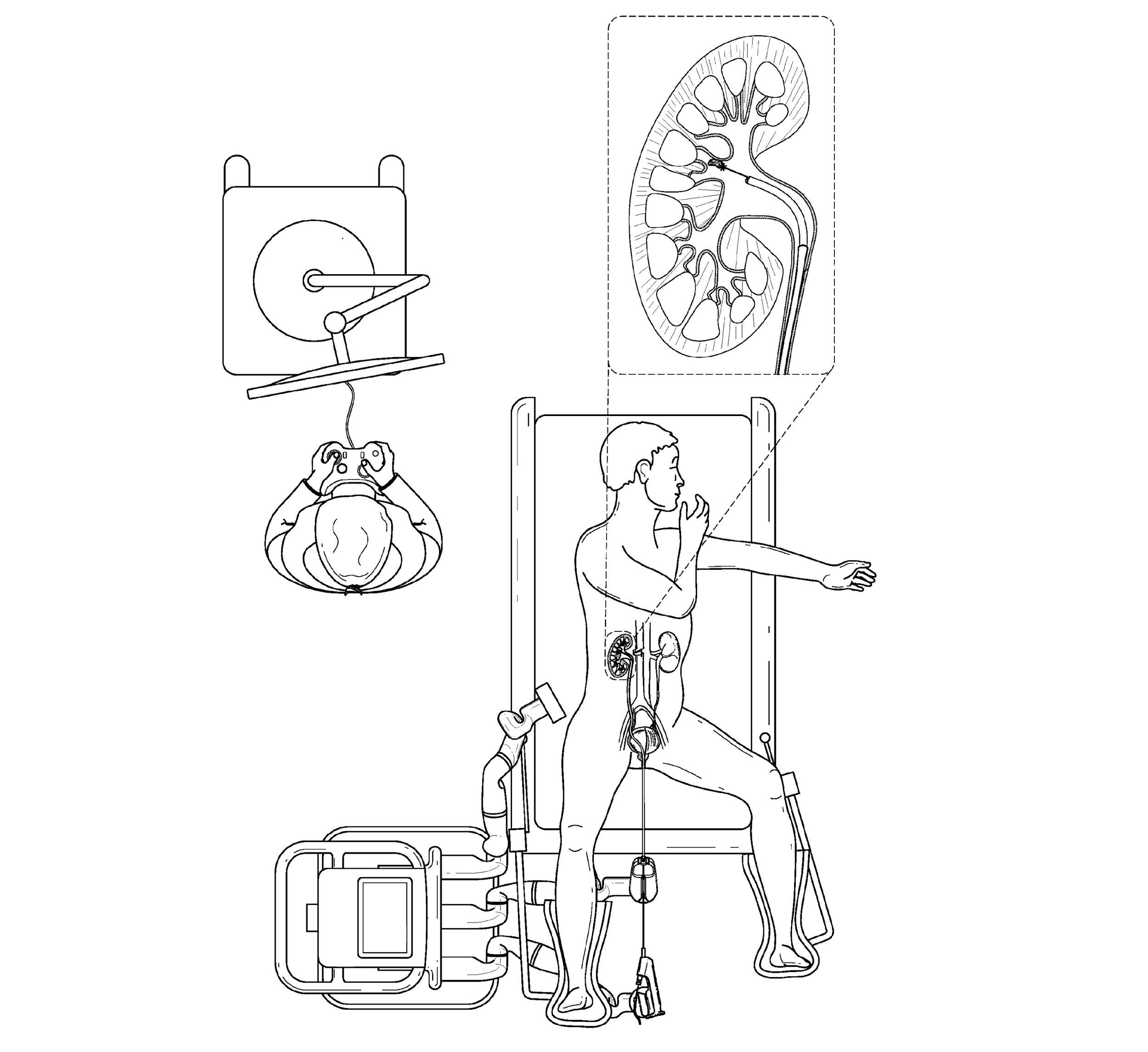
Part of a system
The ureteroscope driver is a complex mechanism that only has value as part of a whole.
A multi-armed robot positions the device relative to the patient and manipulates the device input splines to drive the shaft of a ureteroscope placed inside the device center channel.
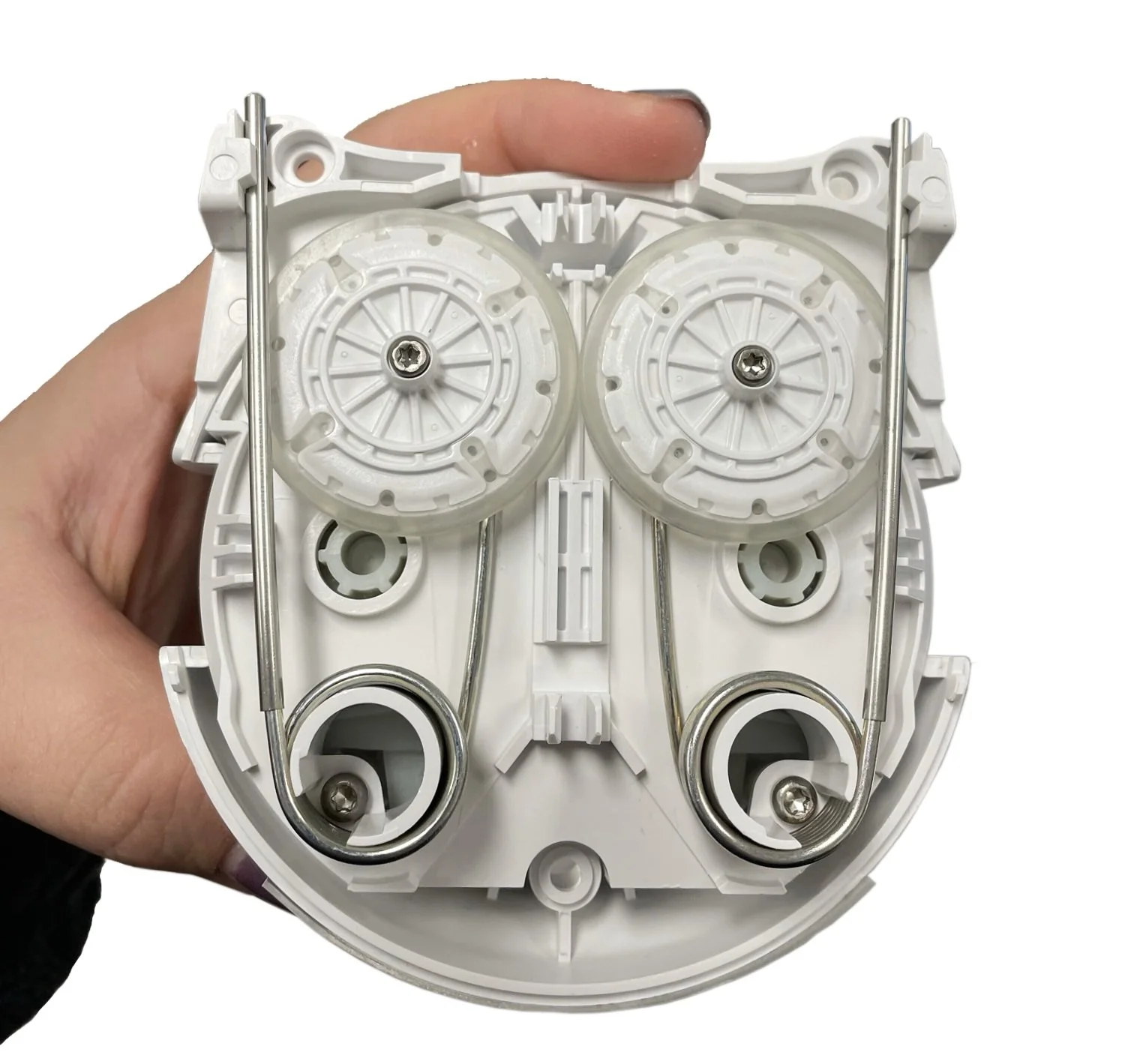
Over-molded wheels grip a flexible shaft and turn in tandem to drive the shaft forward/back.
As the lead (and only) project engineer, I drove this device from early conception to design verification.
3D printed, assembled, and tested 6 successive functional prototypes in lockstep with other mating/interfacing subsystems and systems
Developed engineering specifications and requirements, DFMEA
Translated the functional design to a production design, including developing 17 unique custom-molded components
Worked with industrial designers, engineering contractors, molding houses, manufacturing engineers, quality engineers, systems and control engineers, tech leads on mating devices
Developed Design Verification protocols, test methods, and test fixtures to prove safety and efficacy of the final device
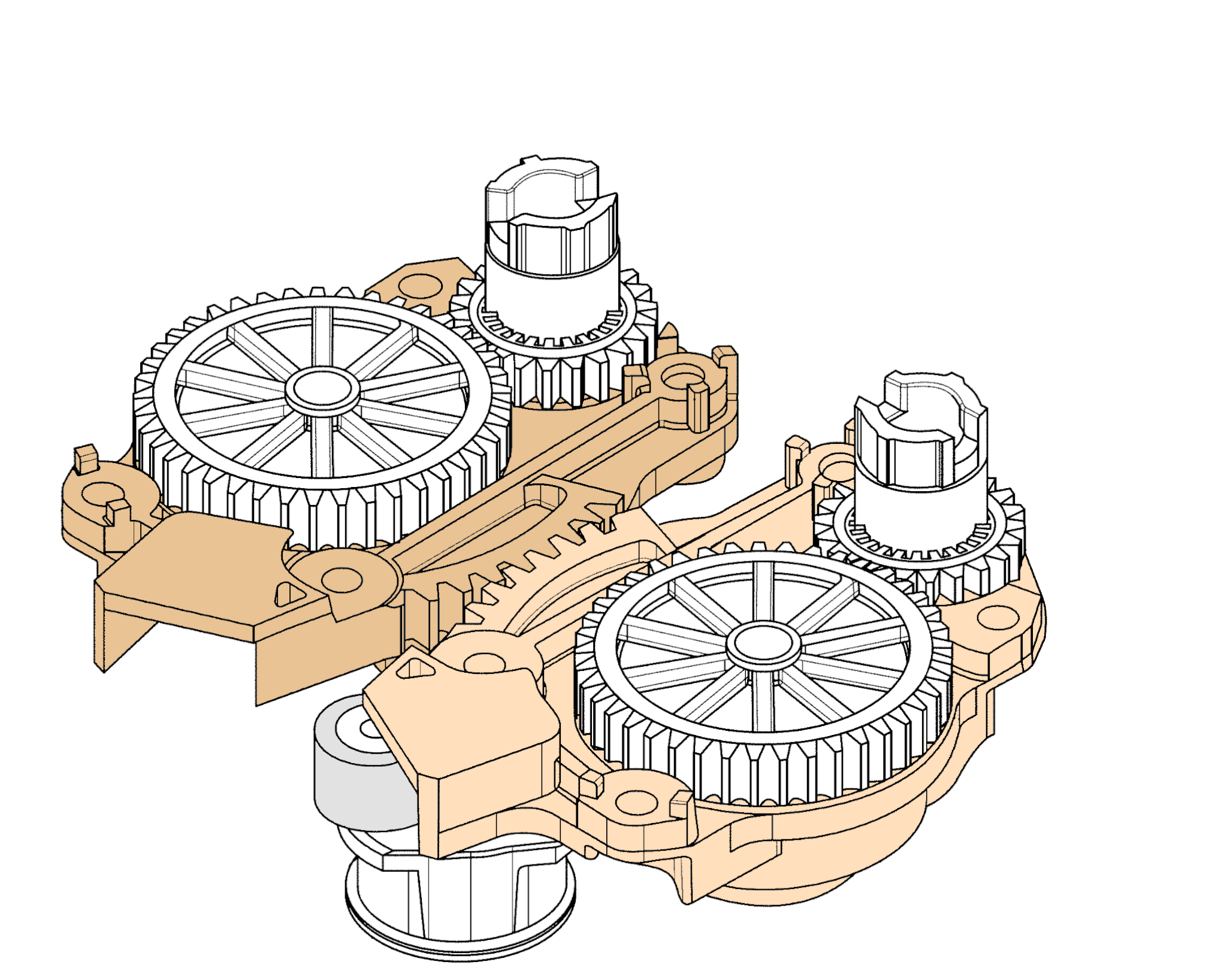
Planetary gears and a mirroring butterfly gear
A planetary gear design allows the wheel rotation to remain fully controllable regardless of wheel position, and independent drive of each wheel enables finer feedback to the robotic system.
A butterfly gear between gear trains permit a single robotic input to control both wheel positions mirrored about the centerline of the device.